模拟量控制系统目录
在dcs应用中,模拟量输入输出主要链接什么设备? 还有数字量输入输出通常接什么设备?
模拟量控制系统

模拟量控制系统是一种对锅炉、汽轮机及辅助系统的有关模拟量参数进行连续闭环控制的自动控制系统。这个系统通过将模拟量转换成数字量,然后对这些数字量进行处理和控制,以实现对被控模拟量参数值维持在设定范围或按预期目标变化的目的。
在模拟量控制系统中,PLC(可编程控制器)是重要的组成部分之一。PLC可以通过A/D转换器将模拟量转换为数字量,然后对这些数字量进行采样和量化,最终实现对被控模拟量的控制。
以上信息仅供参考,如有需要,建议您咨询专业技术人员。
在dcs应用中,模拟量输入输出主要链接什么设备? 还有数字量输入输出通常接什么设备?
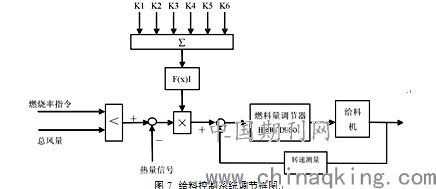
模拟量是连续变化的量,
DCS系统检测现场的工况(温度、压力、流量)
信号按照传递方向分为输入信号和输出信号;
输入信号是从现场到DCS系统的检测信号,如温度、压力、流量、液位、电机运行/停止状态等;
输出信号是从DCS系统到现场的控制信号,如调节阀开度输出、变频器设定输出、电磁阀开关命令、电机启动/停止命令等;
模拟量信号为连续变化的值可以归一化为 0.0~100.0% ,例如温度检测值、电机电流、变频器转速设定等;
数字量信号只有“0”和“1”两种状态(OFF/ON),例如电机运行/停止状态、电机启动/停止命令等;
各类信号的常见应用:
模拟量输入(AI):4~20mA输入、1~5V输入、PT100热电阻、TC热电偶、PI脉冲信号
温度变送器、压力变送器、流量变送器、液位变送器、电机电流、调节阀阀位反馈;
模拟量输出(AO):4~20mA输出
调节阀开度输出、变频器频率设定;
数字量输入(DI):温度开关、压力开关、流量开关、液位开关、按钮、电磁阀全开/全关回讯、限位开关、电机运行状态、备妥信号、故障信号、就地/远程切换信号等;
数字量输出(DO):电磁阀开/关输出、电机启动命令、电机停止命令、指示灯;
常见设备的信号分配:
1:电磁阀:
电磁阀全开/全关回讯 为 数字量输入(DI)
电磁阀开/关输出 为 数字量输出(DO)
2:调节阀:
调节阀阀位反馈 为 模拟量输入(AI)
调节阀开度输出 为 模拟量输出(AO)
3:电机(泵,风机):
电机运行状态、备妥信号、故障信号、就地/远程切换信号 为 数字量输入(DI)
电机启动命令、电机停止命令 为 数字量输出(DO)
4:变送器 为 模拟量输入(AI)
5:各种开关(压力开关、液位开关、温度开关)和按钮 为 数字量输入(DI)
什么是RB试验
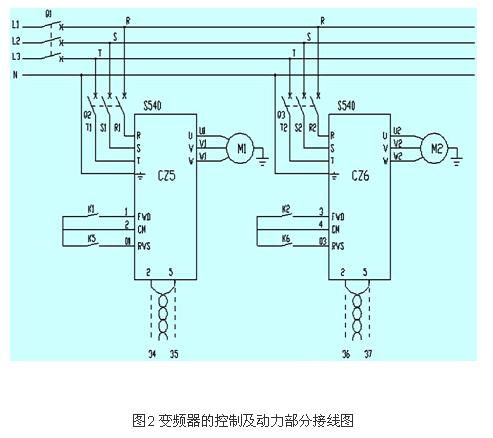
机组RB功能试验
1.RB试验的目的
RB试验的主要目的是检验火电机组在辅机发生故障跳闸锅炉出力低于给定功率时,自动控制系统将机组负荷快速降低到实际所能达到的相应出力的能力,是对机组自动控制系统性能和功能的考验。
2 机组RB试验应具备的条件
2.1 模拟量控制系统,如机组功率控制系统、燃烧控制系统、给 水控制系统、温度控制系统和其他辅助控制系统已正常投用,并经过相应的定值扰动和负荷变动试验,调节品质达到《验评标准》的要求。
2.2 机组功率控制方式应为协调方式,其他几种运行方式(如机跟随、炉跟随)也已投运过,并已进行过负荷变动试验。
运行方式的切换已经过考验,能手动或自动进行无扰切换。
采用滑压运行的机组还需检查滑压运行控制功能。
2.3 锅炉炉膛安全监控系统(FSSS)已经正式投入运行,RB信号至FSSS的联系正常,逻辑关系正确。
2.4 机组保护系统正常投入。
3 RB功能静态试验
3.1 在机组停机的情况下,根据机组设计的功能,依次模拟RB产生的条件,检查负荷运算回路、负荷指令速率变化等RB功能回路,并按经验数据(或设计)初步设定负荷指令变化速率。
3.2 检查RB工况发生后,与其他热控系统如FSSS系统的联系,确认其逻辑功能的正确性。
3.3 检查热控系统与汽机电调或同步器的接口匹配情况。
在RB工况下,有方式切换的系统应检查方式切换功能。
4 RB功能动态试验
机组达到额定出力后,按试验大纲的要求,根据设计的RB功能分项进行动态试验,记录各被调量的动态曲线,RB工况下负荷指令变化率通过试验进行修正最后确定。
通过试验最后确定较合适的各辅机故障跳闸时机组负荷指令变化速率。
5 RB试验时对参数要求
机组RB试验时,参数波动范围不危及机组安全和不引起机组保护动作跳闸,即为合格。
三菱PLC的设计方法
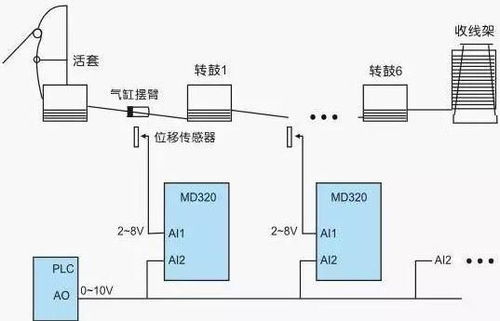
三菱PLC控制系统一般设计方法:
1、分析控制系统的控制要求
熟悉被控对象的工艺要求,确定必须完成的动作及动作完成的顺序,归纳出顺序功能图。
2、选择适当类型的PLC
根据生产工艺要求,确定I/O点数和I/O点的类型(数字量、模拟量等),并列出I/O点清单。
进行内存容量的估计,适当留有余量。
根据经验,对于一般开关量控制系统,用户程序所需存储器的容量等于I/O总数乘以8;对于只有模拟量输入的控制系统,每路模拟量需要100个存储器字;对于既有模拟量输入又有模拟量输出的控制系统,每路模拟量需要200个存储器字。
确定机型时,还要结合市场情况,考察PLC生产厂家的产品及其售后服务、技术支持、网络通信等综合情况,选定性能价格比好一些的PLC机型。
3、硬件设计
根据所选用的PLC产品,了解其使用的性能。
按随机提供的资料结合实际需求,同时考虑软件编程的情况进行外电路的设计,绘制电气控制系统原理接线图。
4、软件设计
(1)软件设计的主要任务是根据控制系统要求将顺序功能图转换为梯形图,在程序设计的时候最好将使用的软元件(如内部继电器、定时器、计数器等)列表,标明用途,以便于程序设计、调试和系统运行维护、检修时查阅。
(2)模拟调试。
将设计好的程序下载到PLC主单元中。
由外接信号源加入测试信号,可用按钮或小开关模拟输入信号,用指示灯模拟负载,通过各种指示灯的亮暗情况了解程序运行的情况,观察输入/输出之间的变化关系及逻辑状态是否符合设计要求,并及时修改和调整程序,直到满足设计要求为止。
5、现场调试
在模拟调试合格的前提下,将PLC与现场设备连接。
现场调试前要全面检查整个PLC控制系统,包括电源、接地线、设备连接线、I/O连线等。
在保证整个硬件连接正确无误的情况下才可送电。
将PLC的工作方式置为“RUN”。
反复调试,消除可能出现的问题。
当试运一定时间且系统运行正常后,可将程序固化在具有长久记忆功能的存储器中,做好备份。
评论列表(0条)